Technological Innovation and Global Strategy for China’s Battery Industry in 2025
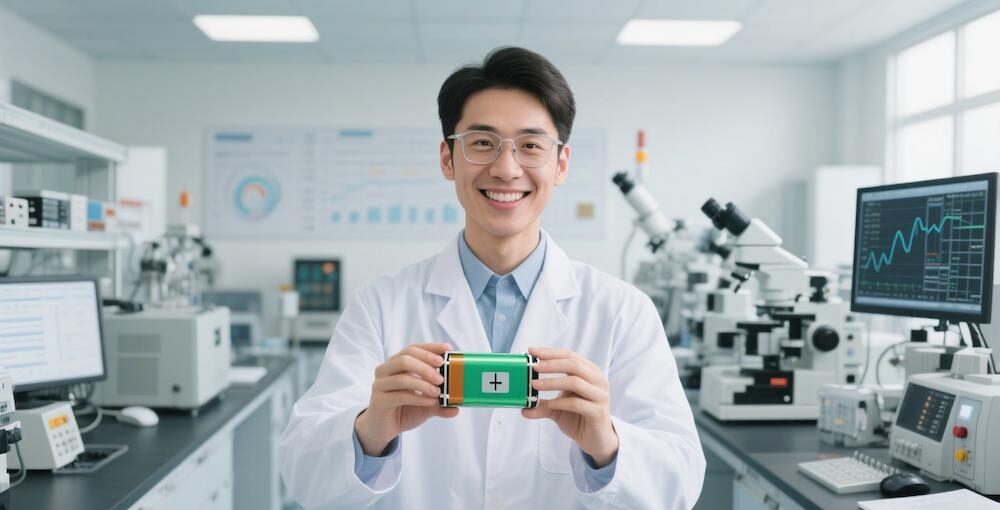
The year 2025 is a watershed year for the development of China’s battery industry. With the formal implementation of the Ministry of Industry and Information Technology’s “Safety Requirements for Power Storage Batteries for Electric Vehicles”, “no fire, no explosion” has changed from a technical vision to a mandatory standard, forcing the whole industry chain to start a technological leap.
New safety regulations and industrial changes have become the most distinctive features of China’s battery industry in 2025. In May this year, the official release of the “most stringent battery standard” completely reshaped the industry’s safety benchmarks.
The most fundamental change in the new national standard is the elimination of the “5-minute window of escape” after thermal runaway, directly requiring the battery system in the full life cycle without fire, explosion6, while adding a simulation of urban road bottoming out accident bottom impact test, requiring the battery pack to withstand the diameter of 30mm steel ball with 150 joules of energy three times after the impact No leakage, no fire and explosion.
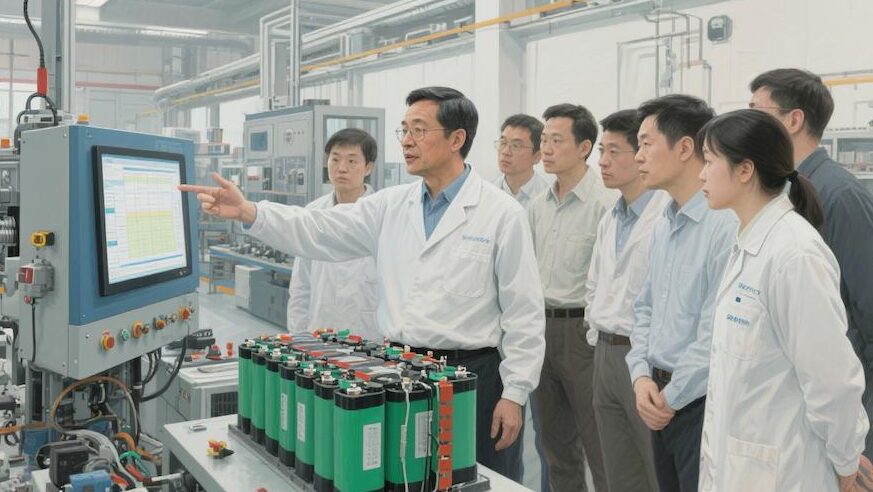
1, the new safety regulations, forcing an industrial revolution
In April 2025, China’s Ministry of Industry and Information Technology (MIIT) issued the Safety Requirements for Power Storage Batteries for Electric Vehicles (GB38031-2025), which caused a huge shock in the new energy industry.1 This mandatory national standard, which will be fully implemented on July 1, 2026, will fundamentally change the technological routes and competitive landscape of China’s battery industry.6 The new national standard has gone beyond the technical requirements of the battery industry.
The technical requirements of the new national standard have surpassed European and American standards, becoming the new benchmark for global power battery safety. In the bottom impact test, the EU standard only requires a single impact, while China’s new national standard increases to 3 times; in the fast-charging cycle test, the U.S. UL standard only requires 50 cycles, while China’s new national standard is raised to 300 times.
This change stems from a deep reflection on safety issues. 2024, China’s new energy vehicles reported more than 550 fire accidents, an average of 1.5 per day, of which power battery failure was the main cause.1 The new standard will drive the industry from a “range race” to a “safety priority”. The new standard will drive the industry to shift from “race for range” to “safety first”, and safety technology innovations such as thermal runaway monitoring system and flame retardant materials will become the key to the competition among automobile enterprises.
2, solid-state breakthroughs, mass production process accelerated
Under the mandatory requirements of “no fire, no explosion”, the industrialization of solid-state batteries has accelerated significantly. The flammability of traditional liquid electrolyte is difficult to meet the requirements of the new national standard, and solid-state batteries have ushered in the development opportunity by virtue of its non-flammable solid-state electrolyte characteristics6.
In June 2025, Vonergy announced that its 60Ah sulfide all-solid-state battery is scheduled to be delivered in small batches to strategic partners by the end of the year, with an energy density as high as 400-500Wh/kg, which is 2-3 times higher than that of traditional liquid lithium batteries. This breakthrough puts China at the forefront of the world in the commercialization of all-solid-state batteries.
Ouyang Minggao, academician of the Chinese Academy of Sciences, pointed out that: from the point of view of technology research and development, the all-solid-state battery industry will focus on solid-state electrolyte from 2025 to 2030; high-capacity composite anode from 2030 to 2035; and high-capacity composite positive electrode from 2035 to 2040.
Domestic enterprises are accelerating the layout in the field of solid-state batteries:
Ganfeng Lithium: the first domestic company to realize the mass production of solid state battery pilot line, the first generation of 200 million watt-hours production line has been put into production
Ningde Times: cooperation with Peak Flying Aviation to develop eVTOL solid state batteries, is expected to realize the semi-solid state technology breakthrough in 2025
BYD: relying on the group’s capital and industry chain resources, Ningbo plant expansion to enhance the production capacity of solid state batteries
The research institute EVTank predicts that by 2030 the global shipment of solid state batteries will reach 614.4 million tons of battery capacity. Global shipments of solid-state batteries will reach 614.1GWh by 2030, and the penetration rate in lithium batteries is expected to be around 10%.
3, application diversification, scene boundary expansion
With the improvement of battery technology performance and safety standards upgraded, lithium battery application scenarios are breaking through the traditional new energy vehicle field, expanding to more strategic emerging industries.
In the field of low-altitude economy, eVTOL is regarded as the core carrier of the industry to put forward rigid demand for battery energy density, its battery energy density requirements for 300Wh/kg and above, this benchmark must rely on semi-solid and all-solid state battery technology breakthroughs. Fu can science and technology has been the head of the United States eVTOL customers, the domestic head of the flying car customer fixed point, its second generation of semi-solid-state battery energy density of more than 330Wh/kg, is promoting the head of the humanoid robotics company to send samples.
Humanoid robotics has become one of the most promising application scenarios for solid-state batteries. Solid-state batteries can not only significantly enhance the robot range time, coupled with its non-flammable, non-corrosive, non-volatile properties, can maximize the safety of robots working in indoor environments.
In the field of energy storage, with the global proportion of wind and light distribution storage increased to more than 25%, China’s large base project mandatory distribution storage policy to promote the domestic installed capacity of new energy storage in 2025 exceeded 80GW. industrial and commercial energy storage into the era of parity, the cost of kilowatt-hour electricity (LCOS) fell to 0.6 yuan / Wh below, the European and American household storage market, the average installed capacity of households up to 15kWh.
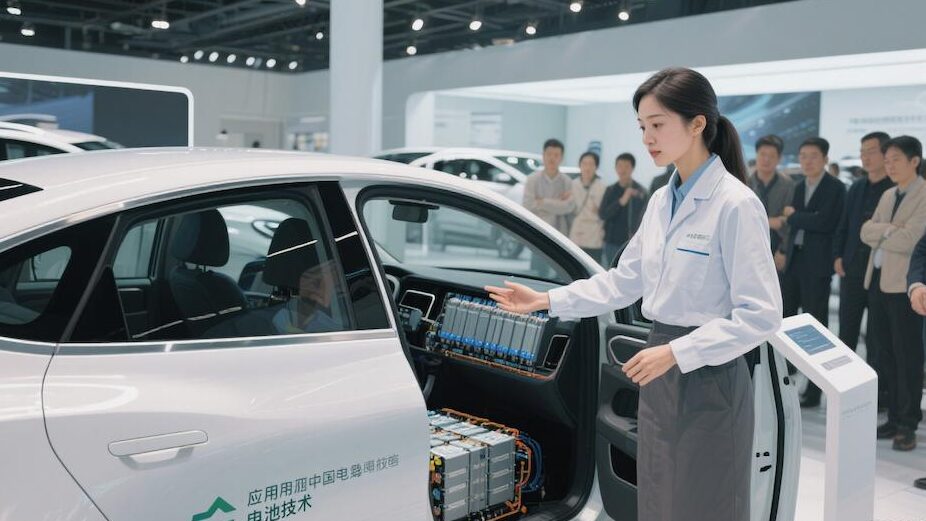
4, material revolution, core technology breakthroughs
In order to meet the requirements of the new national standard and improve energy density, China’s battery industry has realized a series of breakthroughs in the material system and manufacturing process.
In the field of electrolyte, the composite technology route has become the mainstream solution:
Tsing Tao Energy adopts the “oxide + halide + polymer” composite technology path, and is expected to be loaded on SAIC MG and other models on a large scale starting from 2025.
Ningde Times obtained the patent authorization of the preparation method of doped halide solid state electrolyte in January 2025.
Lienergy, Hunan Enjie, BYD and FAW are also actively promoting Halide electrolyte route
Positive and negative electrode material systems have also made significant progress:
Anode materials: lithium manganese iron phosphate (LMFP) market share exceeded 20%, monocrystalline high-nickel ternary adapted to 800V fast-charging platform
Negative electrode innovation: silicon-based negative electrode penetration rate exceeded 15%, lithium-metal negative electrode entered the pilot phase10
In terms of the preparation process, the core of the solid-state battery process technology lies in the preparation of the solid-state electrolyte and the film-forming technology, which is mainly divided into two types: the wet process and the dry process:
The wet process prepares electrolyte film through coating, drying and other processes, which is simple to operate and easy to scale up production
The dry process prepares self-supporting electrolyte film through fibrillating treatment and milling molding, which reduces the proportion of solvents and improves ion transport performance
5. Recycling and upgrading, sustainable closed-loop construction
With the surge in lithium battery production and the peak of decommissioning, recycling has become a key link in the sustainable development of the industry. China has clearly set a target of a recycling rate of over 30% by 2025 in the Guidelines for the High-Quality Development of the Lithium Battery Industry .
The U.S. Department of Energy is funding Pure Lithium in 2025 to develop lithium metal recycling technology. The company’s “Brine to Battery” process significantly reduces recycling costs and environmental impacts by extracting lithium metal directly from discarded batteries, bypassing the multiple steps of the traditional recycling process.
Leading Chinese companies are establishing complete resource recycling systems:
Greenpeace and Huayou Cobalt have built the world’s first closed-loop “battery recycling – material recycling – battery remanufacturing” base.
Ningde Times and BYD have set up a nationwide recycling network for decommissioned batteries, which ensures the recycling of key materials.
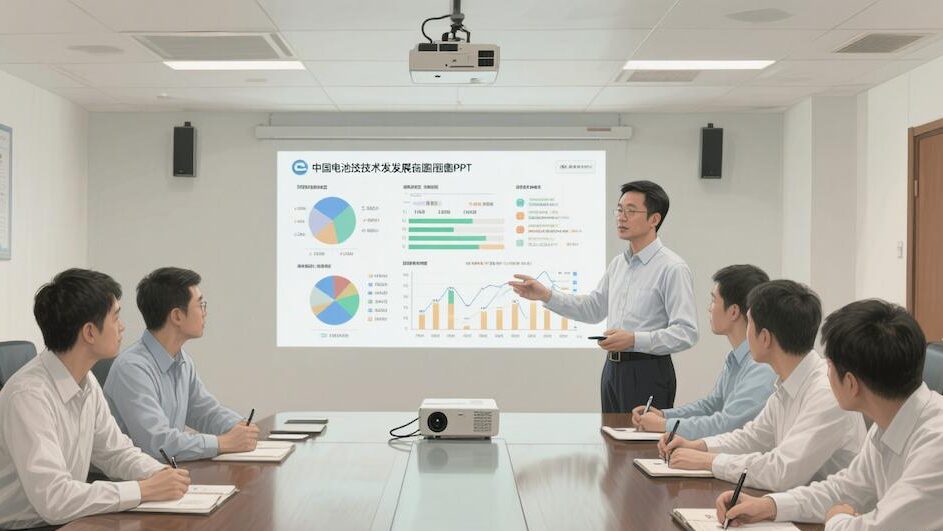
6, global competition, the rise of Chinese standards
In terms of globalization layout, Chinese battery enterprises are facing a dual-track policy environment of carbon tariff and localization, accelerating the reconstruction of the global industrial chain.
Ningde era, LG new energy global dual oligopoly pattern is solid, combined market share of more than 55% 10. second-tier manufacturers are competing for niche markets: BYD blade battery dominated the A-class car market, in the new aviation bound to the Guangzhou automobile EAN and other high-growth customers.
The policy environment in Europe and the United States has changed significantly:
EU carbon border tax (CBAM) officially covers lithium batteries, and localization ratio is required to be raised to 70%.
U.S. IRA bill increases local sourcing of key minerals, and 80% is required by 2025.10
Chinese battery companies break through trade barriers through technology licensing model. The 40GWh capacity of Ford-Ningde Times Michigan plant went into full production in 2025, becoming a model of Sino-US battery technology cooperation.
It is worth noting that the technical requirements of China’s new national standard for power batteries have surpassed the existing regulations in Europe and the United States, and its innovative testing methods and systematic evaluation system have attracted the attention of international counterparts and may become the industry’s reference standard.This “technological overtaking” has pushed China’s battery industry to shift from ‘following’ to “leading”. This “technological overtaking” has pushed China’s battery industry from ‘following’ to “leading”.
7, the future outlook, challenges and opportunities co-exist
Looking forward to the next five years, China’s battery industry is facing three key technical directions:
All-solid-state battery mass production process optimization is still the primary challenge. Solid – solid interface is still the main solid-state battery card point, electrode and electrolyte between the existence of micron-level gaps, interface impedance up to 100 Ω level, much higher than the liquid battery ten Ω level. This leads to slow charging and discharging, limited energy density, limited cycle life and other issues.
Cost control is the key to industrialization. Currently, the cost of semi-solid-state batteries has dropped to below $1/Wh, while the production cost of full-solid-state batteries remains high. Scale production and new material development will be the main path to reduce costs.
Resource security faces geopolitical challenges. The price of lithium, nickel and other resources may enter a tight balance again in 2025. Chinese companies are responding to policy changes in resource countries, such as nickel export restrictions in Indonesia and the trend of nationalization of lithium mines in Africa, through the integrated layout of “mining-smelting-battery”.
On the application front, eVTOL and robotic battery solutions will become the focus of innovation. The comprehensive requirements of humanoid robots for battery safety, energy density and cycle life will promote the accelerated maturity of new battery systems.
The global demand for lithium batteries is expected to maintain a compound annual growth rate of more than 25% during 2025-2030, and the trillion-dollar market is being reconfigured by the technological revolution and safety standards.
When safety and innovation become the twin engines of industrial development, China’s battery industry is shifting from scale expansion to quality leadership. The life line of defense constructed by the new national standard, the energy density leap initiated by solid-state batteries, and the technological discourse in the global supply chain all point to a safer, more efficient, and more sustainable energy future.
This industrial revolution driven by the “China Standard” will not only reshape the local market landscape, but also define the next chapter of global electrification14.
Battery technology in 2025 is a year of rapid development