Impact of High Specific Surface Area LFP on Battery Manufacturing in 2025
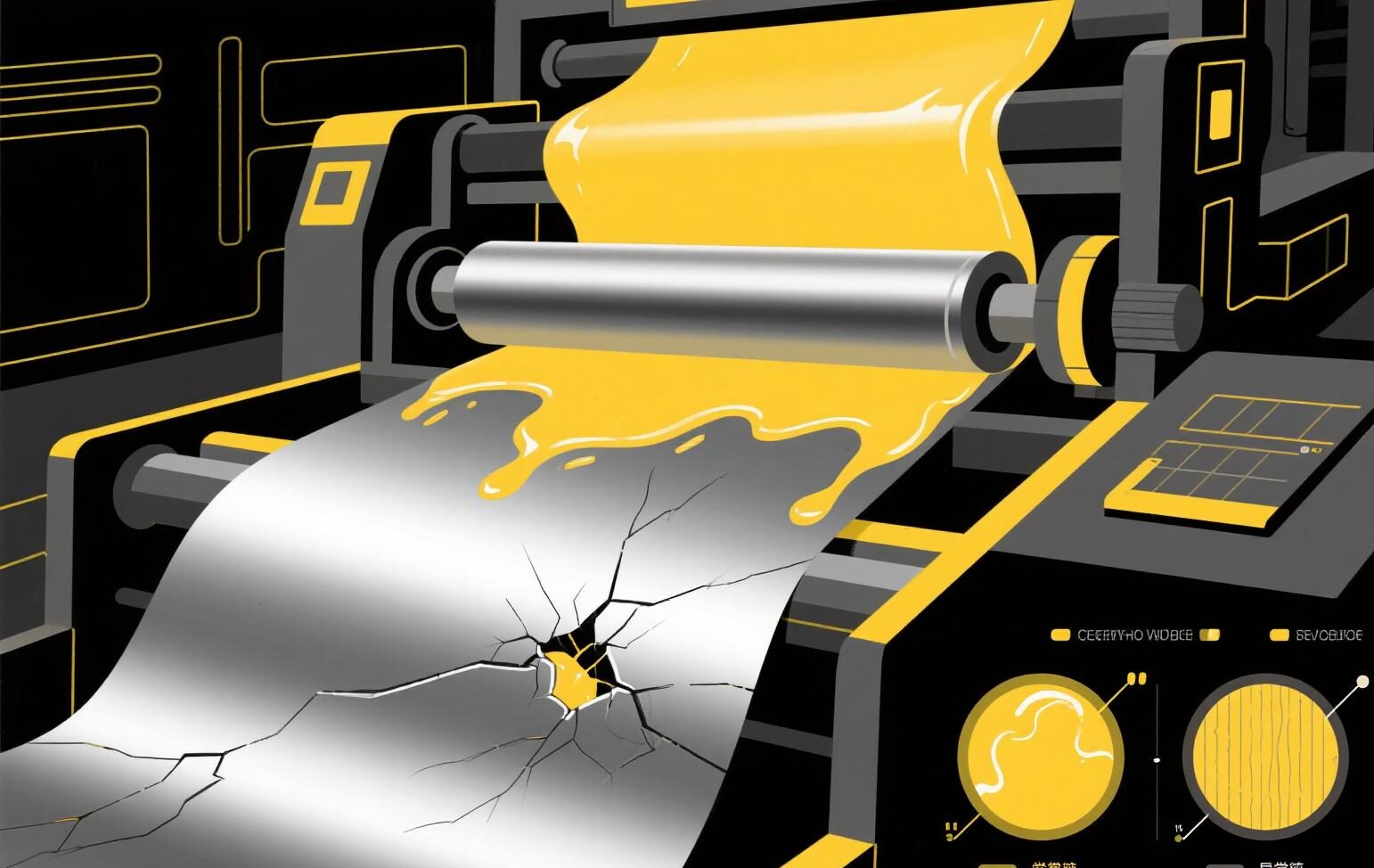
Lithium iron phosphate (LFP) remains a staple in power batteries and energy storage due to its safety and long cycle life. However, battery manufacturers often face challenges: switching to a new batch of LFP material can cause fluctuations in slurry quality, electrode performance, and final battery properties—directly impacting production efficiency and causing significant economic losses.
The root cause? Specific surface area (SSA)—a key indicator of particle size and a critical factor in battery manufacturing capabilities.
What Determines LFP’s Specific Surface Area?
LFP’s specific surface area is determined by particle size and carbon content, balancing electrical performance and compaction density. Most LFP particles are nano/submicron-sized, and smaller particles typically mean higher SSA. Additionally, carbon coating creates porous structures: higher carbon content increases pores, boosting SSA.
Parameter | Market Mainstream Range |
Specific Surface Area | 10~15 m²/g |
Carbon Content | 0.9%~1.5% |
How High SSA Disrupts Battery Production
Lithium battery electrodes consist of active materials (90%~98%), conductive agents, binders, and additives. Slurry preparation—mixing these components into a stable suspension—involves three stages: wetting, dispersing, and stabilizing. High SSA LFP disrupts this process, cascading into issues across production steps.
1. Impact on Mixing Process
High SSA LFP causes agglomeration, increased stirring resistance, and jelly-like gel formation:
- Agglomeration: High surface energy drives particles to bond via van der Waals forces or hydrogen bonds, forming uneven clumps.
- Viscosity spikes: High SSA particles absorb more NMP solvent, thickening the slurry and reducing flowability.
- PVDF network entanglement: Nano-LFP particles embed into PVDF structures, creating physical gels.
Consequences: Longer mixing times, higher energy consumption, shorter equipment lifespan, lower solid content, increased NMP usage, and rising production costs.
2. Impact on Coating Process
High SSA LFP slurries often exhibit severe viscosity rebound and gelation, leading to:
- Poor leveling: Slurries fail to spread evenly on aluminum foil, causing defects like uneven surface density, scratches, cracks, and white spots—amplified after drying.
- Narrower coating window: High viscosity increases flow resistance in slit dies, risking blockages. Frequent cleaning reduces stable coating speed, lowering efficiency.
3. Impact on Calendering Process
- Amplified surface defects: Coating irregularities (stripes, orange peel texture) become stress points under high pressure, causing cracking, powder loss, or web breaks.
- Thickness inconsistency: Uneven coating thickness leads to over-compression in thin areas and under-compression in thick areas, harming battery performance consistency.
- Binder distribution issues: Uneven binder migration (e.g., surface enrichment) weakens adhesion, worsening powder loss during calendering.
4. Impact on Subsequent Processes
- Slitting/die-cutting: Increased burrs and dust from pre-existing powder loss raise short-circuit risks.
- Stacking/winding: Defective electrodes (micro-cracks, uneven edges) risk breakage under tension, reducing alignment accuracy.
- Final battery performance: Poor conductivity, interface contact issues, and uneven active material utilization cause higher internal resistance, capacity loss, and poor rate performance. Defects like micro-shorts may lead to abnormal self-discharge.
Key Outcomes of High SSA LFP
Aspect | Impact |
Product Quality | Poor electrode appearance, inconsistent thickness/density, increased internal resistance, shortened cycle life, safety risks (e.g., internal short circuits). |
Production Efficiency | Reduced coating speed, frequent downtime for cleaning/rework, increased equipment maintenance. |
Manufacturing Costs | Lower yield, higher raw material waste, elevated energy/equipment costs. |
While high SSA enhances lithium ion diffusion, reversible capacity, and rate performance, it poses significant manufacturing challenges. As new energy vehicles demand higher energy density, nano-sized, high-compaction LFP materials exacerbate these issues. Current solutions focus on cathode formula optimization, especially adding high-efficiency dispersants to improve slurry properties.
Addressing this bottleneck requires synergies between material modification, process innovation, and equipment upgrades. Breakthroughs in these areas will accelerate the large-scale application of high-energy-density LFP batteries, meeting diverse market needs.