Impact of copper foil thickness on lithium battery performance
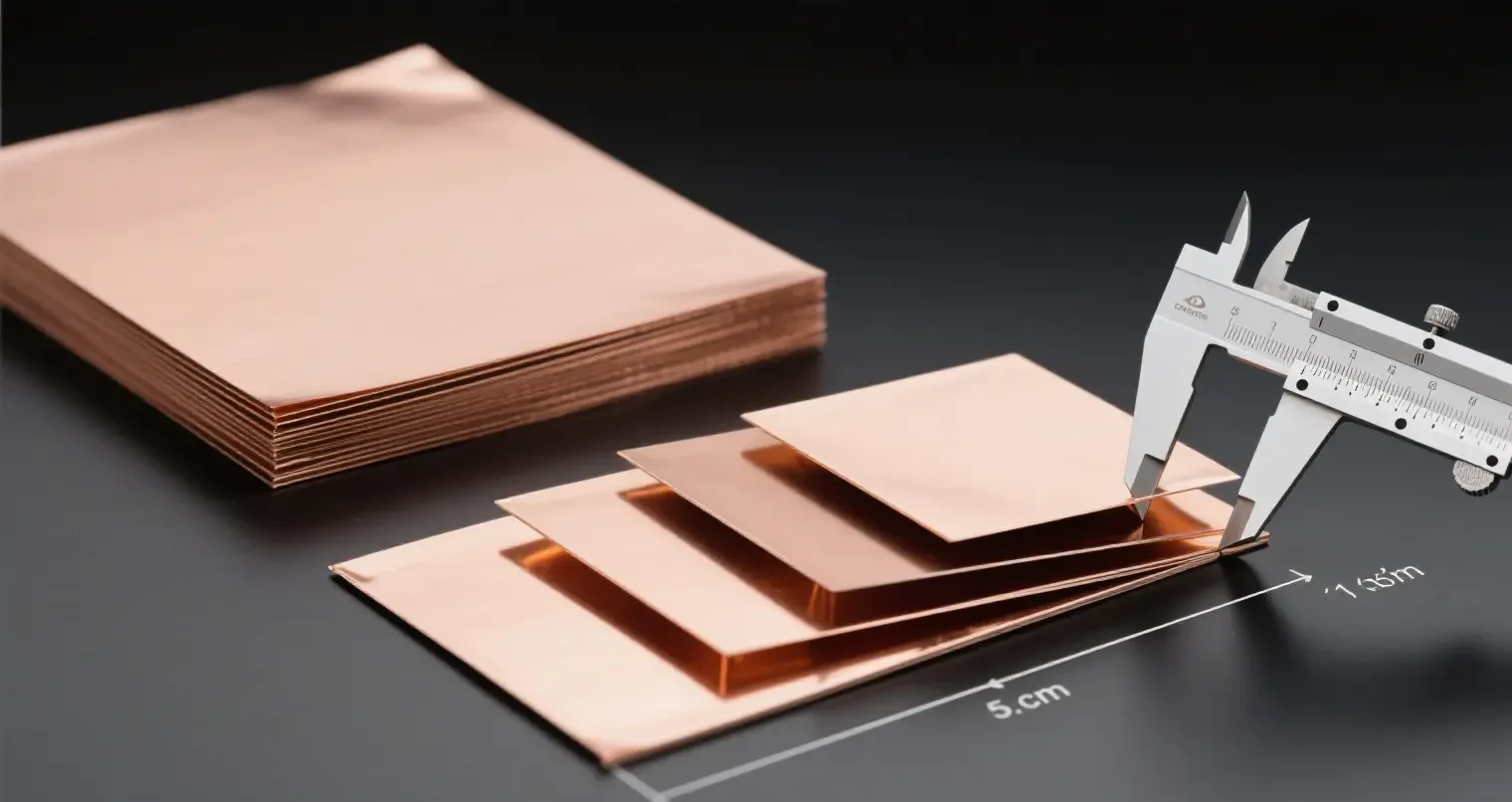
Copper foil is used as the anode carrier and collector of lithium-ion batteries, and the thickness of copper foil plays a crucial role in lithium batteries, which affects the performance, safety and cost of lithium batteries. Next we come to a detailed analysis of the lithium battery copper foil thickness is specifically how to affect the battery, designed to provide reference for the majority of lithium battery practitioners and enthusiasts.
I. the impact of the battery energy density
1. Mass energy density
copper foil as a negative electrode collector, itself does not participate in the electrochemical reaction, the thinner its thickness, the proportion of active substances in the battery (such as graphite) can be increased accordingly. For example, if the thickness of copper foil is reduced from 10μm to 6μm, the overall mass of inactive material in the battery will be reduced by about 40%, and more active materials can be accommodated in the same volume, which can theoretically increase the mass energy density by 5%-8%.
2. Volume energy density
The thickness advantage of thin copper foil directly reduces the volume of inactive materials inside the battery. Take 18650 batteries as an example, using 8μm copper foil compared to 12μm copper foil, the utilization of space inside the cell can be increased by about 3%, and the volumetric energy density can be increased accordingly.
II.Influence on battery internal resistance and multiplier performance
1. DC Resistance (DCR)
The DC resistance of copper foil is inversely proportional to its thickness. According to Ohm’s law, the resistance of 10μm copper foil is about twice that of 5μm copper foil. Measurement data show that the internal resistance of lithium batteries with 10μm copper foil is about 60mΩ at 25℃, while the internal resistance of batteries with 5μm copper foil can be reduced to less than 45mΩ, which is conducive to the reduction of heat loss in the process of charging and discharging.
2. Multiplier performance
Thin copper foil has lower resistance, which makes the current distribution more uniform during high-current charging and discharging and avoids localized overheating. For example, the capacity retention rate of batteries with 6μm copper foil can reach 85% at 10C multiplication rate, while that of batteries with 10μm copper foil is only 78%. Especially in high-power power batteries, thin copper foil improves the multiplication rate performance more significantly.
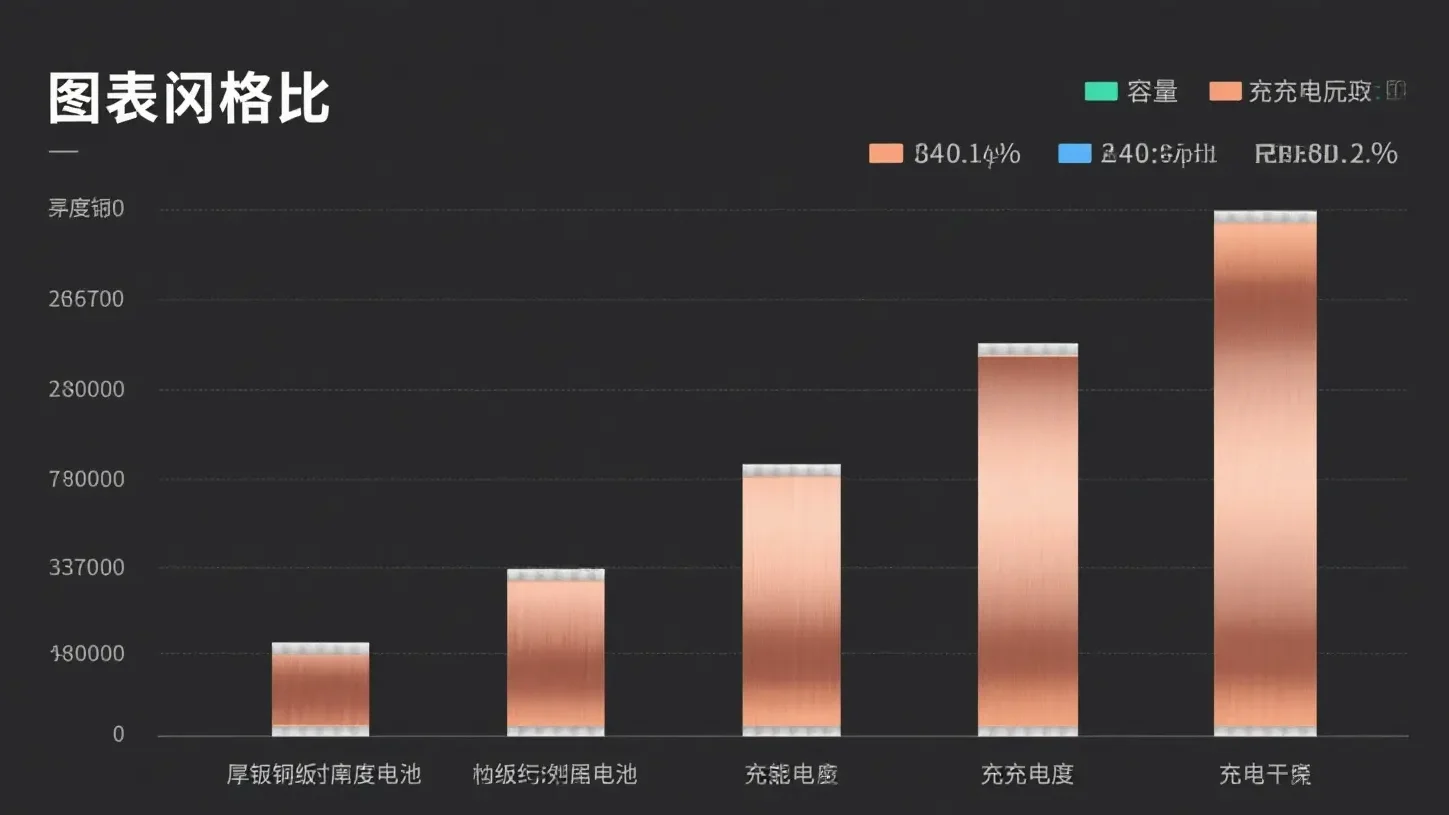
III.nfluence on battery cycle life
1. Mechanical Strength and Cycle Stability
The thickness of copper foil is positively correlated with the mechanical strength: the tensile strength of 10μm copper foil is about 280MPa, while the tensile strength of 4μm copper foil is reduced to 220MPa. Too thin copper foil is prone to micro-cracks in the process of rolling or cycling of the pole piece, which leads to poor contact between the collector and the active substance, and the rise of internal resistance. Experiments show that the capacity retention rate of the battery with 4μm copper foil is 82% after 500 cycles, while that of the battery with 8μm copper foil can reach 88%.
2. Risk of lithium dendrite penetration
Copper foils with thickness less than 5μm are more likely to be penetrated by lithium dendrites if lithium dendrites grow on the negative electrode during long-term cycling, leading to internal short circuit. Research shows that the internal short-circuit failure rate of batteries with copper foils below 5μm is about 30% higher than that of batteries with 8μm copper foils in the late cycle.
IV.Impact on Battery Safety
1. Thermal Conduction and Heat Dissipation
The thickness of copper foil affects the internal thermal conduction efficiency of the battery. 10μm copper foil has a thermal conduction rate of about 2W/(m・K), although the increase in thickness is limited to enhance the thermal conduction capacity, the heat dissipation path of the thinner copper foil is shorter in the case of heat concentration under high current, and the risk of localized overheating needs to be compensated for by the structural design (e.g., by increasing the heat-conducting adhesive).
2. Performance in pinning test
Thick copper foil (e.g. 10μm) can delay the occurrence of internal short circuit in the pinning test, because the copper foil itself has a certain mechanical barrier effect. Test data shows that the peak thermal runaway temperature of the battery with 10μm copper foil is 210℃ during the pinning test, while the peak temperature of the battery with 6μm copper foil reaches 240℃, which is a higher risk of thermal runaway.

V. Impact on production cost and process
1. Material cost
The thickness of copper foil has a linear relationship with the cost: the unit price of 8μm copper foil is about 120 RMB/kg, and the unit price of 4μm copper foil can be more than 200 RMB/kg due to the complexity of the production process. Taking 1GWh power battery as an example, using 6μm copper foil will increase the material cost by about 800,000 RMB compared with 10μm copper foil.
2. Production process adaptability
1. Rolling process: thin copper foil (<5μm) is prone to uneven thickness when rolling, requiring roll accuracy of ±0.5μm, and the investment in equipment is 50% higher than that of conventional production lines.
2. Coating process: when thin copper foil carries active substances, the control of coating tension is more stringent, and fluctuations in tension of more than 5N will lead to folding of the pole piece, and the yield rate will drop from 95% to less than 85%.
VI. Conclusion
The choice of copper foil thickness is a comprehensive balance of battery energy density, performance, safety and cost: consumer electronics tends to be extremely thin to improve portability, power batteries need to optimize the overall performance in the 6-8 μm range, and energy storage focuses more on the long-cycle reliability of thicker copper foils. With the development of coating technology and composite collector, the boundary of copper foil thickness is gradually broken, but process stability and cost control are still the key to industrialization.