In-depth analysis of solid state battery equipment industry chain
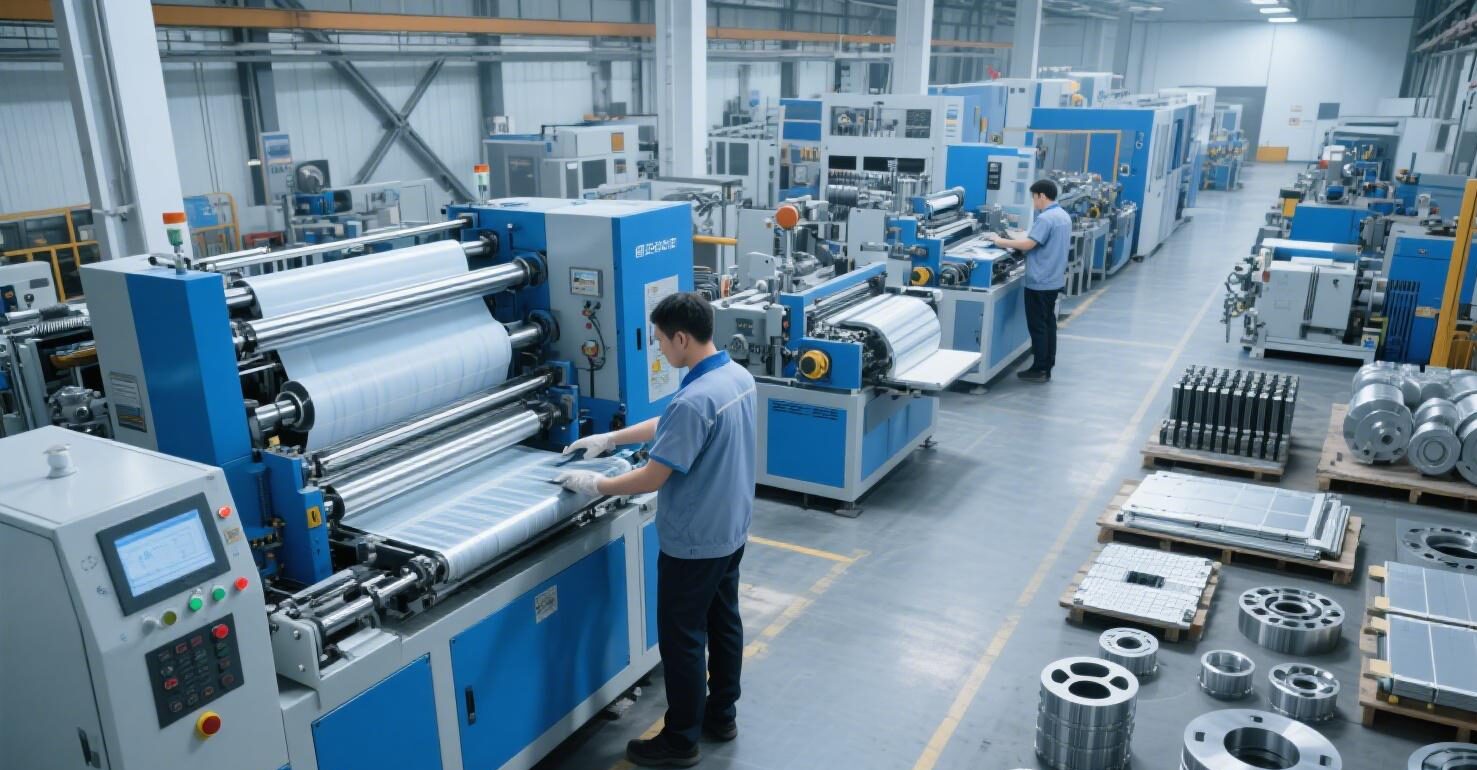
Core logic: solid state battery industrialization follows the path of “equipment first → material follow-up → scene landing”, and 2025-2027 is the key period for mass production verification. Equipment link is the first to benefit from the construction of production lines, solid-state battery equipment industry chain value release pioneer.
I.the value of equipment reconstruction: technology upgrades to drive the cost of leapfrogging
1 traditional liquid battery: single GWh equipment investment of about 2-220 million yuan
2 semi-solid-state battery: equipment update rate of more than 60%, single GWh value volume increased by 30% to 280 million yuan (new dry coating, interface optimization equipment)
3 full-solid-state battery: subversive changes in the production process, a single GWh equipment investment jumped to 4-6 billion yuan (dry electrode + isostatic pressure equipment dominated)
cost difference root cause: All-solid-state battery to cancel the electrolyte injection link, but the new dry film, high-pressure encapsulation and other high-precision equipment, equipment complexity has increased significantly.
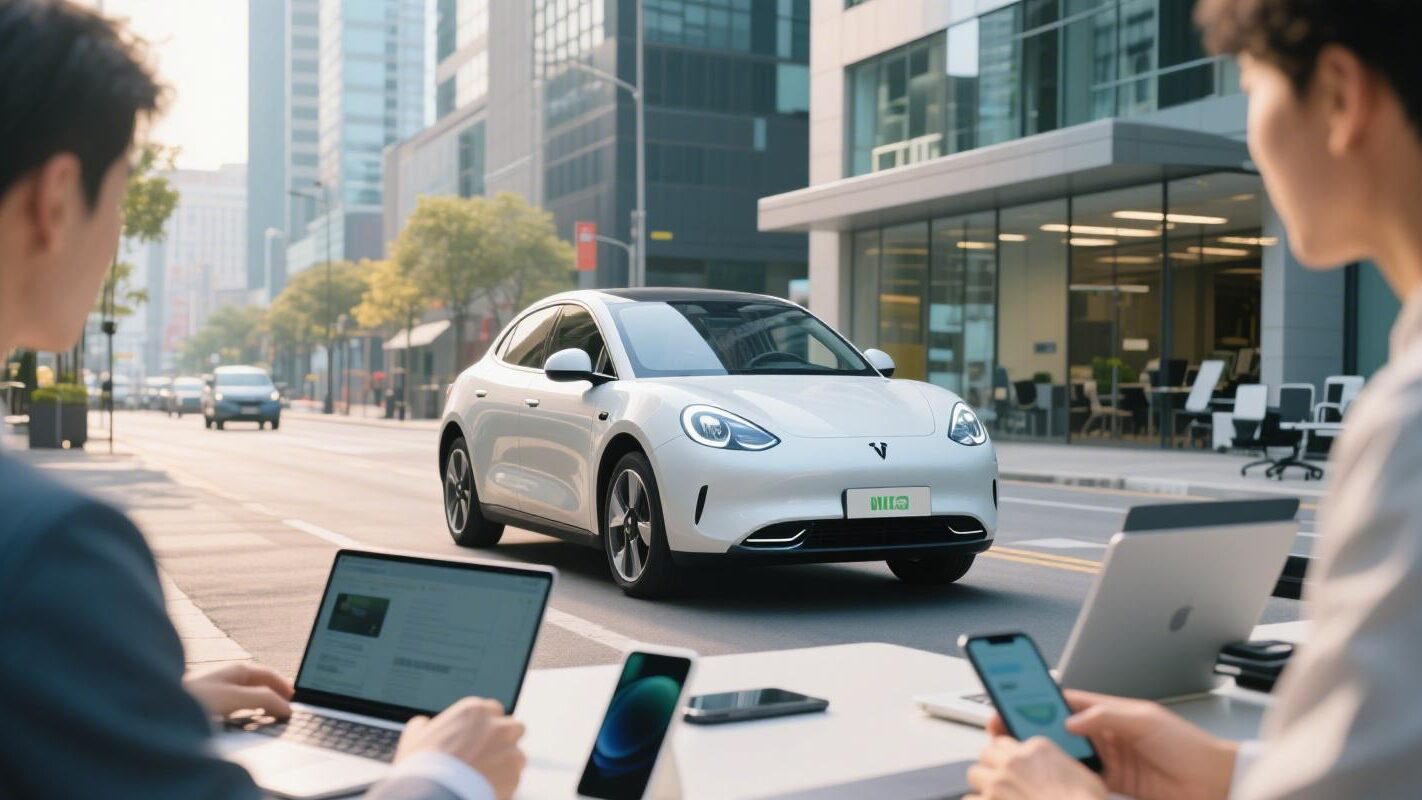
II.equipment technology change: three major process system reconstruction
Front-end equipment: dry process leading material preparation
– Dry electrode technology: instead of the traditional wet process, the use of dry powder mixing + hot pressing molding, to enhance the electrode energy density by 20%.
Core equipment:
▪ Dry coating machine (width ≥ 1000mm, speed 80m/min)
▪ Vacuum evaporation machine (sulfide electrolyte layer thickness accuracy ± 0.1μm)
– Electrolyte preparation: sulfide route relies on evaporation equipment, oxide route adopts casting equipment
Mid-stage equipment: laminating and isostatic pressing technology instead of winding
– Stacker: Adapt to multi-layer stacking structure of solid state battery with yield increased to 95%.
– Isostatic press: 600MPa high pressure to eliminate solid-solid interface gaps, interface impedance reduced by 40% (Ningde Times, BYD core supplier: Naknor)
Back-end equipment: high-pressure synthesis and precision testing
– High-voltage chemical composition cabinet: charging cut-off voltage increased to 5V (4.2V for traditional liquid batteries)
– X-ray detector: Identify cracks in the electrolyte layer at the micron level (detection accuracy ≤ 10μm)
– Laser welding machine: sealing tolerance upgraded to 0.5mm, preventing deliquescence of sulfide electrolyte.
III.the head of the enterprise competition pattern: technology positioning and order verification
company | technical barrier | Order Progress | mass production timetable |
---|---|---|---|
Pilot Intelligence | The world’s only full line delivery capability | Orders of $400-500 million in 2025 (SK, Toyota, etc.) | 2026-2027年 |
Nakonor (city in Buskerud, Norway) | Rolling accuracy ±1μm (global leader) | Ningde Times / BYD order exceeds 1.2 billion yuan | 2026year |
Liyuanheng (city in Hong Kong) | Sulfide complete line equipment (GAC project) | Won the head enterprise whole line project, 2025Q3 delivery | 2026year |
starfish | Lithium metal solid state battery complete line program | Xinjie Energy 2GWh order ($400 million) | 2025the end of the year |
Mannheimstedt (city in the Netherlands) | Dry film-forming equipment (Samsung supplier) | 50 million dollars in orders for 2024 | 2026year |
Market share distribution: Pilot Intelligence (70% of the whole line equipment), Nakonor (60% of the roll pressing equipment), Liyuanheng (15% of the middle and back section equipment).
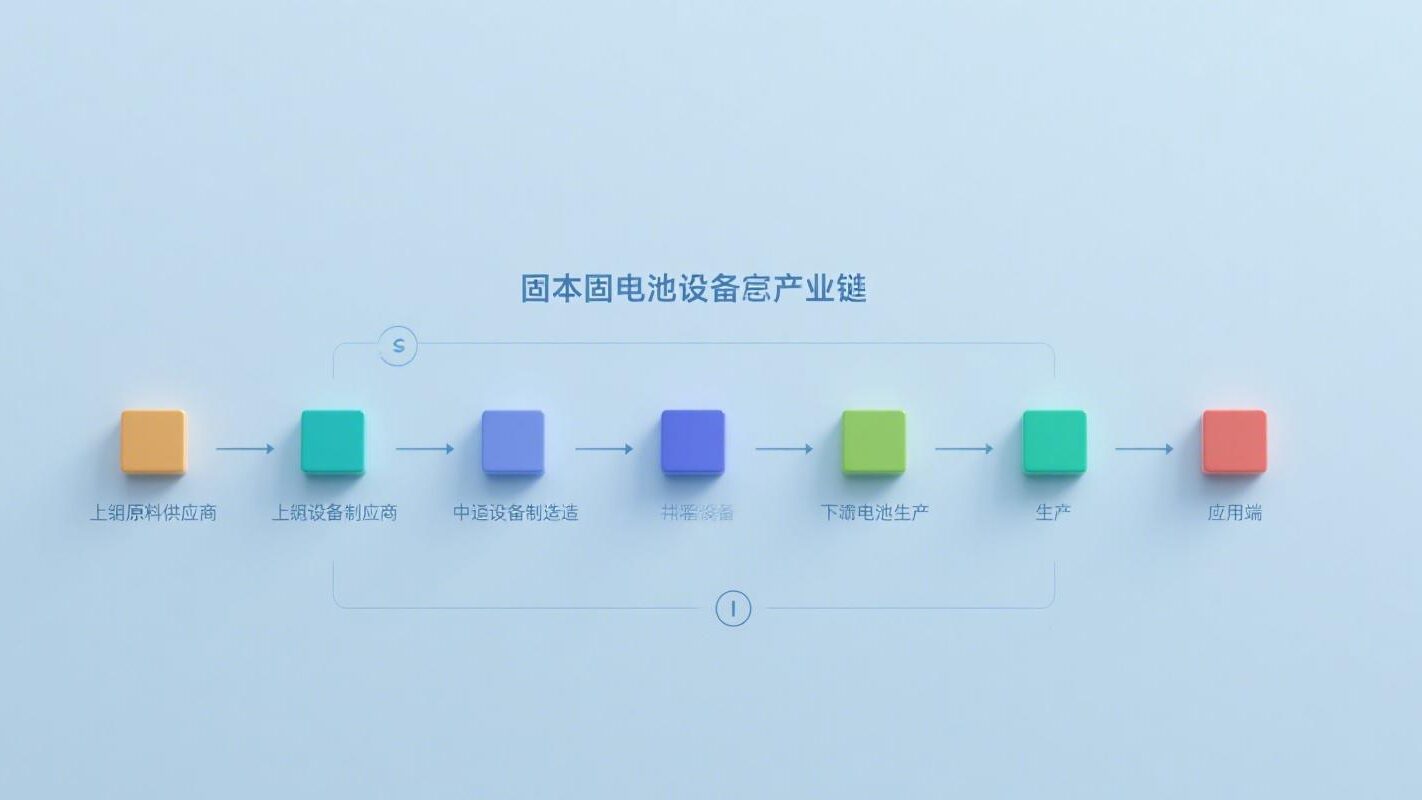
IV. Investment Logic and Risk Warning
Core track:
Complete line integrators (Pilot Intelligence): benefiting from production expansion by overseas customers (Toyota 20GWh capacity by 2027)
Dry process equipment vendors (Mannstar, Winhope Technology): preferred bidder for semi-solid state battery installation wave
High-pressure formation equipment (Hangke Technology): certain demand for back-end process upgrades
Risk Tips:
Risk of technology iteration: Chloride electrolyte breakthrough may overturn the existing sulfide equipment system
Overcapacity: planned capacity of over 200GWh in 2025, actual demand is only 50GWh
Geopolitics : EU carbon tariffs increase the cost of exports (42 euros / ton)
V. Industry trends: from equipment upgrades to scene landing
2025-2026: semi-solid state battery equipment dominant (dry coating + stacking machine demand explosion)
2027-2030: full-solid state equipment discharge (isostatic press + vapor deposition equipment CAGR of 120%)
Emerging Scenarios:
Low Altitude Aerial Vehicle (LAV) Battery: Yihang Intelligent EH216-S equipped with customized solid-state battery (20 take-offs and landings safety standard)
Humanoid Robot Battery: Ubiquiti Walker X lasts 12 hours (Qingtao semi-solid state battery)
“Before the soldiers and horses move, the food and grass go first” – -Advance layout of the equipment segment is the strategic fulcrum to grasp the dividends of the solid-state battery industry. Head enterprises have built a moat through technology patenting (90% equipment autonomy of Pilot Intelligence), and deep customer binding (Ningde Times associated transactions of 8.5 billion yuan). New entrants need to achieve differentiated breakthroughs in niche areas (such as the halide electrolyte equipment of Xinyu people), in order to share the incremental space in the 100 billion market.