Lithium-ion battery pole piece defect mapping
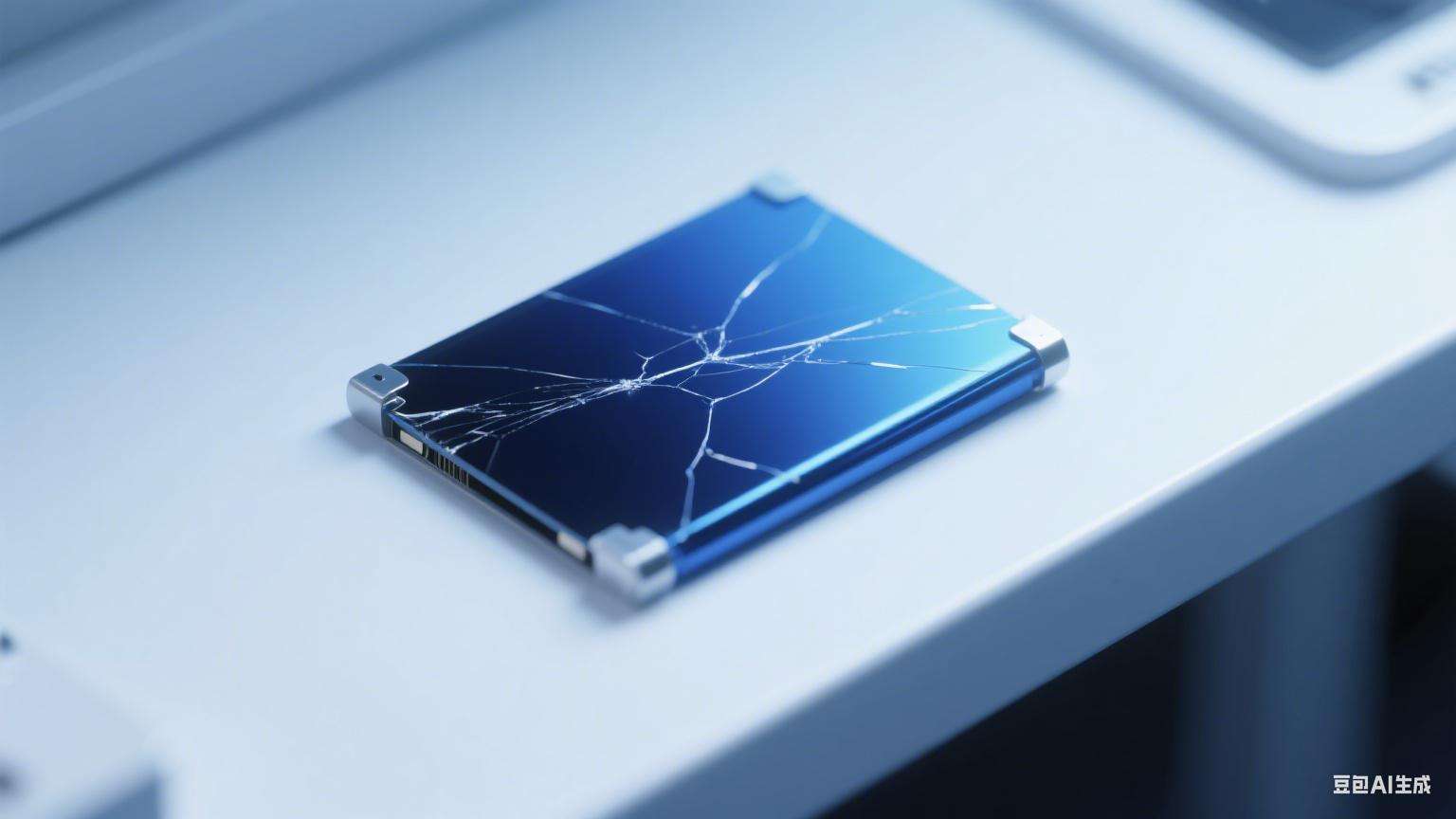
Lithium-ion battery pole piece manufacturing is a key process in the battery production process, specifically including the preparation of slurry, pole piece coating and drying, pole piece roll compaction, and pole piece cutting. In the battery wafer preparation process, more and more online inspection technologies are adopted to effectively identify manufacturing defects, reject defective products, and provide timely feedback to the production line to automatically or manually make adjustments to the production process and reduce the defective rate. The following issues are of particular concern:
1) What defects may be generated in the electrode manufacturing process?
2) What is the impact of these defects on the charge/discharge cycle of lithium-ion batteries?
3) How do defects change the performance of lithium-ion batteries in terms of Coulombic efficiency, multiplicative performance and cycle life?
4) Are there any corresponding microstructural changes in the impaired performance of defective wafers?
Currently, for the pole piece defects, the defect detection and automatic pole piece selection techniques are studied on the one hand, and the effect of defects on battery performance is studied on the other hand, e.g.:
[1] Common defects in lithium battery pole piece extrusion coating
[2] Lithium battery pole piece defect detection and its impact on electrochemical performance
[3] Positive electrode defects have to be discarded? Not necessarily!
In this paper, we share some of the literature and our own actual work in the lithium battery pole piece defects map, collect the various defects and problems encountered, make a pole piece defects atlas, welcome to add.
[1] Negative electrode surface agglomerates particles
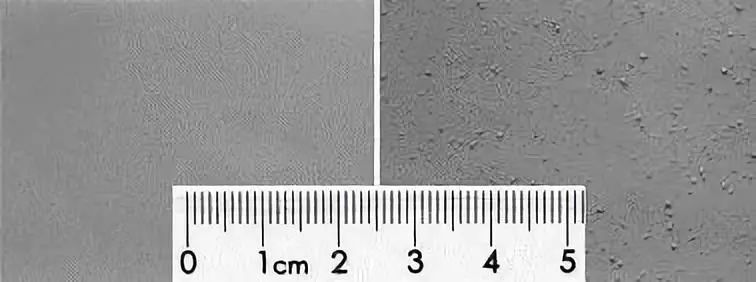
Formulation: Spherical graphite + SUPER C65 + CMC + distilled water Macroscopic morphology of two different mixing processes: smooth surface (left) and the presence of a large number of small particles on the surface (right)
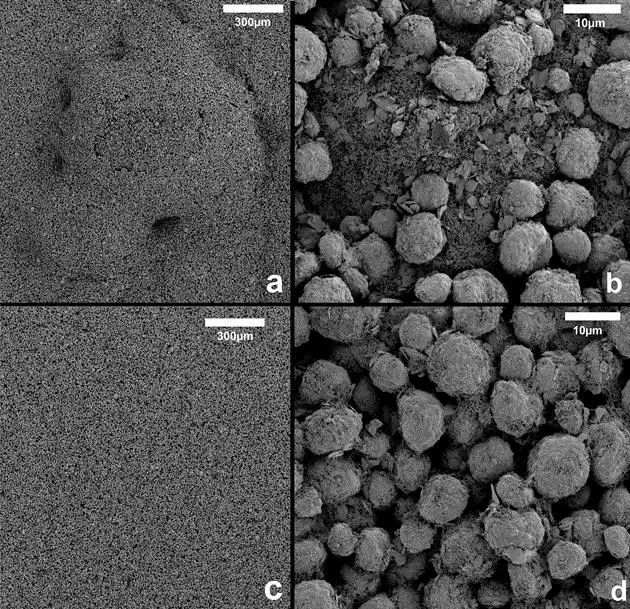
Formulation: spherical graphite + SUPER C65 + CMC/SBR + distilled water Enlarged morphology of small particles on the surface of the electrode sheet (a and b): agglomerates of conductive agent, not fully dispersed Enlarged morphology of a smooth surface electrode sheet: fully dispersed and uniformly distributed conductive agent [Bitsch B,Willenbacher N, Wenzel V, et al. Impact of Mechanical Process Engineering onthe Fabrication Process of Electrodes for Lithium Ion Batteries[J]. ChemieIngenieur Technik. 2015, 87(4). 466-474.]
[2] Anode surface agglomerate particles
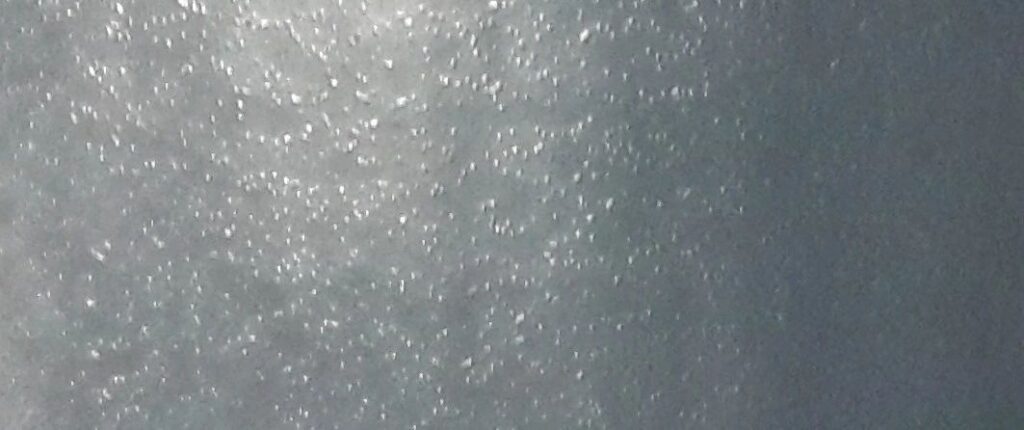
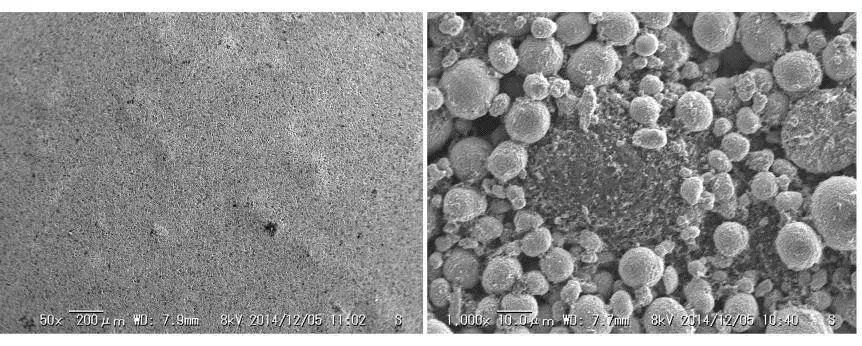
Formulation: NCA+acetylene black+PVDF+NMP
During the mixing process, the environmental humidity is too high, which leads to the jelly state of the slurry, the conductive agent is not completely dispersed, and there are a large number of particles on the surface of the pole piece after roll pressing.
[3] Cracking of water-based pole piece
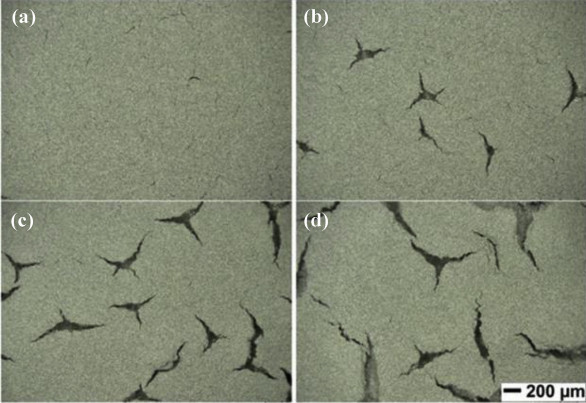
Formulation: NMC532/carbon black/binder= 90/5/5 wt%, water/isopropyl alcohol (IPA) solvent
Optical photographs of cracks on the surface of the electrodes, with coating densities of (a) 15 mg/cm2 , (b) 17.5 mg/cm2 , (c) 20 mg/cm2 and (d) 25 mg/cm2 , respectively, with thicker electrodes being more prone to cracking. . [Du Z, Rollag K M, Li J,et al. Enabling aqueous processing for crack-free thick electrodes[J]. Journalof Power Sources. 2017, 354: 200-206.]
[4] Surface shrinkage of electrodes
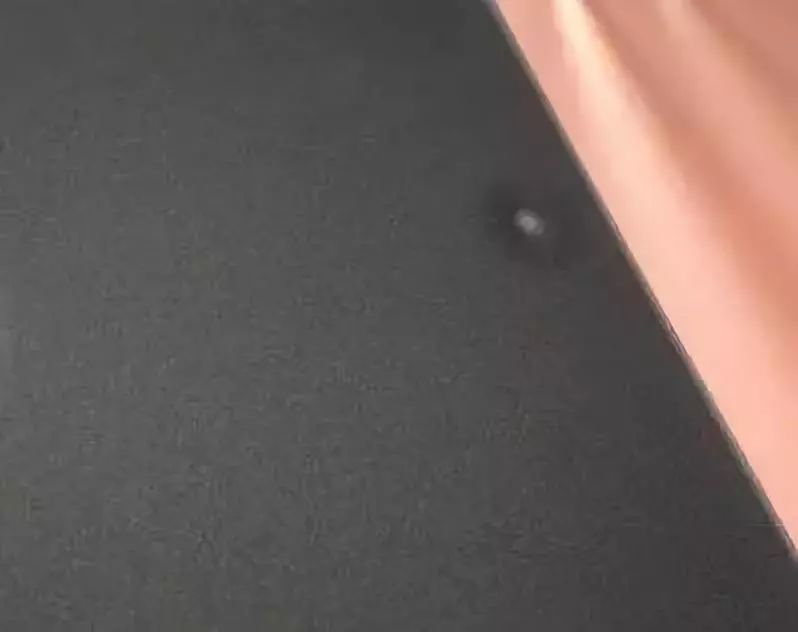
Formulation: flake graphite + SP + CMC / SBR + distilled water foil surface exists leading to contaminant particles, particles at the surface of the wet film exists in the region of low surface tension, the liquid film to the particles around the emissive migration, the formation of shrinkage holes point defects.
[5] Scratches on the surface of the pole piece
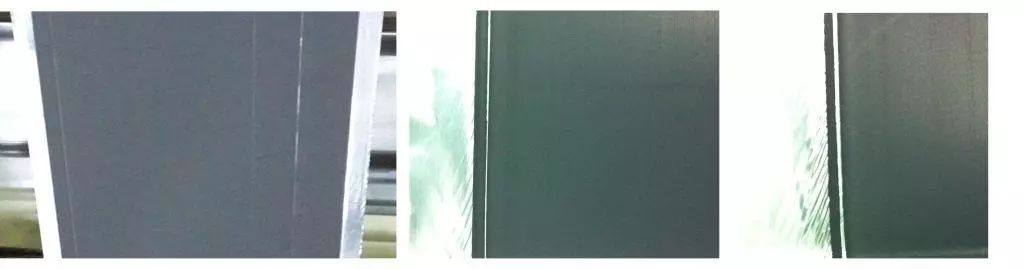
Formulation: NMC532+SP+PVdF+NMP
slit extrusion coating, the presence of large particles at the edge leads to leakage of foil scratches on the surface of the pole piece.
[6] Coating vertical stripes
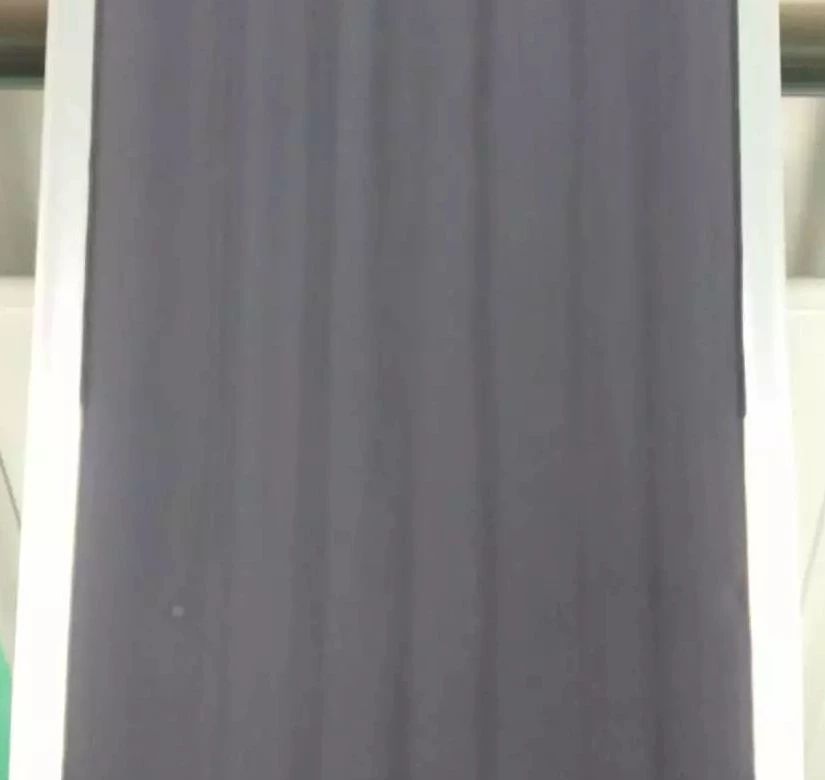
Formulation: NCA+SP+PVdF+NMP
At the late stage of transfer coating, the viscosity of the slurry water absorption rises, the coating is close to the upper limit of the coating window, the slurry leveling is poor, and vertical stripes are formed.
[7] Roller cracks in the undried area of the pole piece
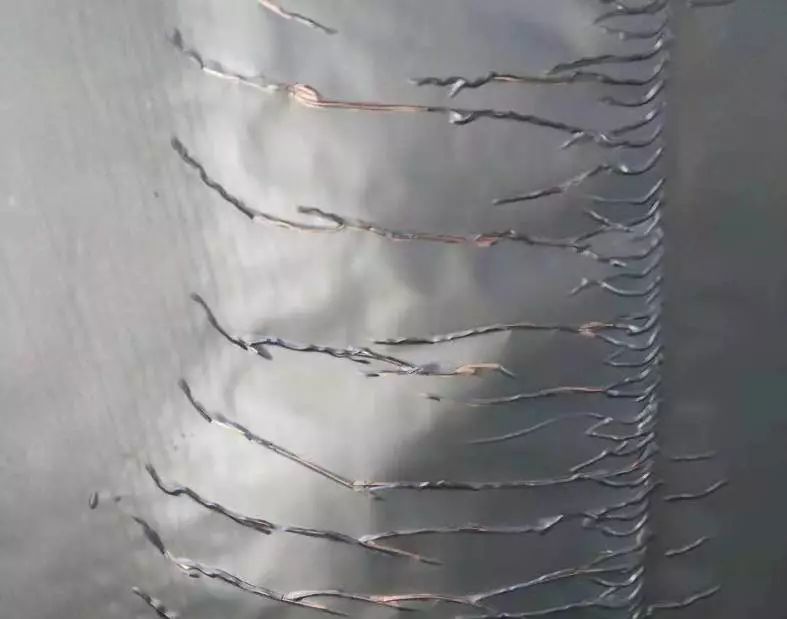
Formulation: flake graphite + SP + CMC/SBR + distilled water
When coating, the middle area of the pole piece was not completely dry, and the coating migrated when rolled, forming strip cracks.
[8] Folding at the edge of the pole sheet during roll pressing
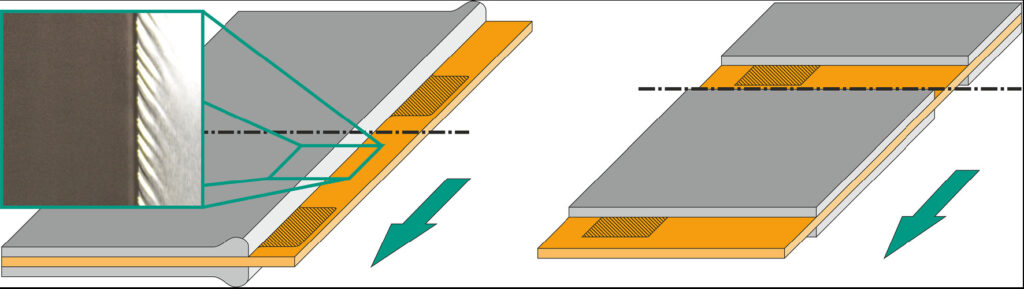
Coating forms a thick edge phenomenon, roll-pressing type, with wrinkles at the edges of the coating [Schmitt, M., et al., Anexperimental and analytical study on intermittent slot die coating ofviscoelastic battery slurries. Journal of Coating Technology and Research, 2015. 12(5): p. 927-938.]
[9] Negative slit coating and foil detachment
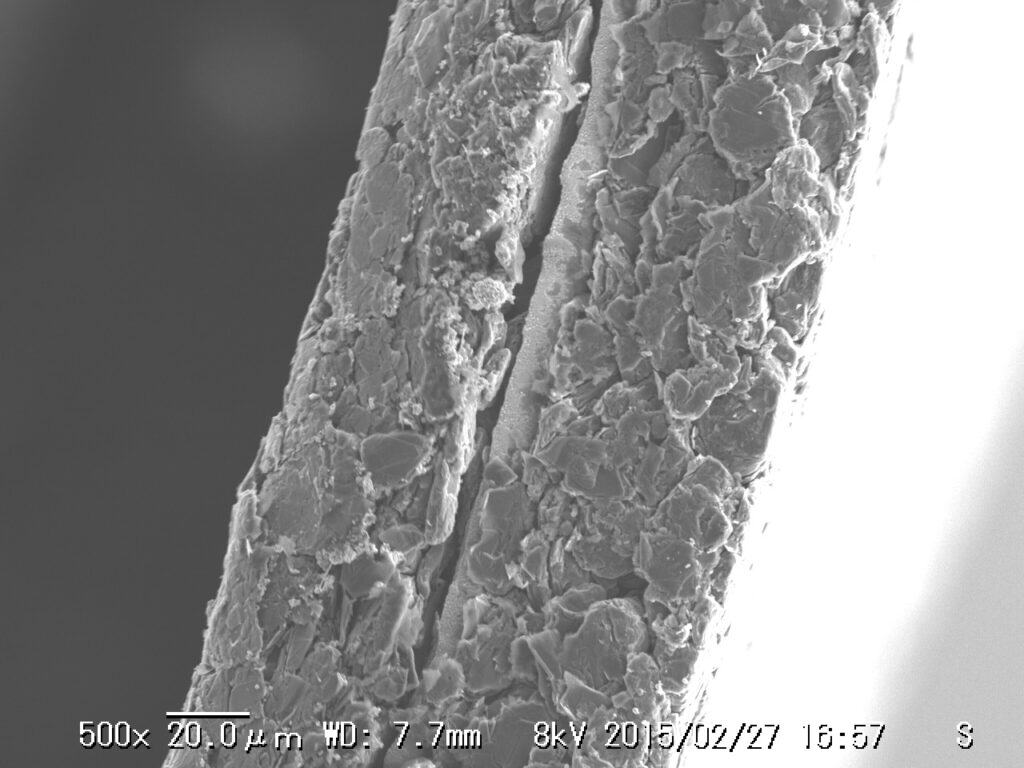
Formulation: natural graphite + acetylene black + CMC/SBR + distilled water, ratio of active substances 96%
The coating is detached from the foil when the pole disc is slit.
[10] Slitting burr of pole disc
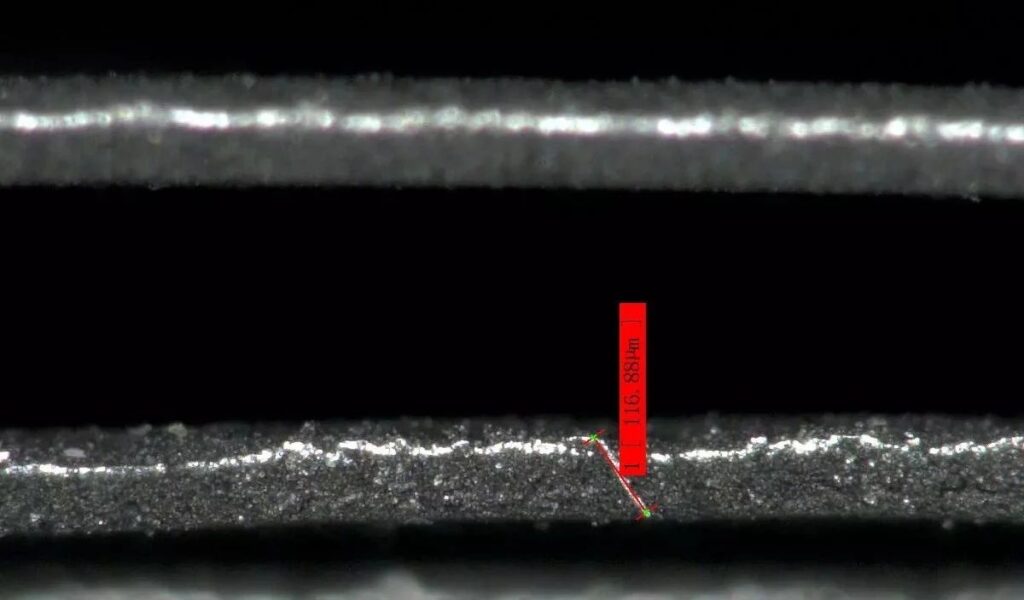
Positive pole disc slitting, due to unstable tension control leads to the formation of foil burrs in the secondary cutting
[11] Wavy edges in slitting of pole piece
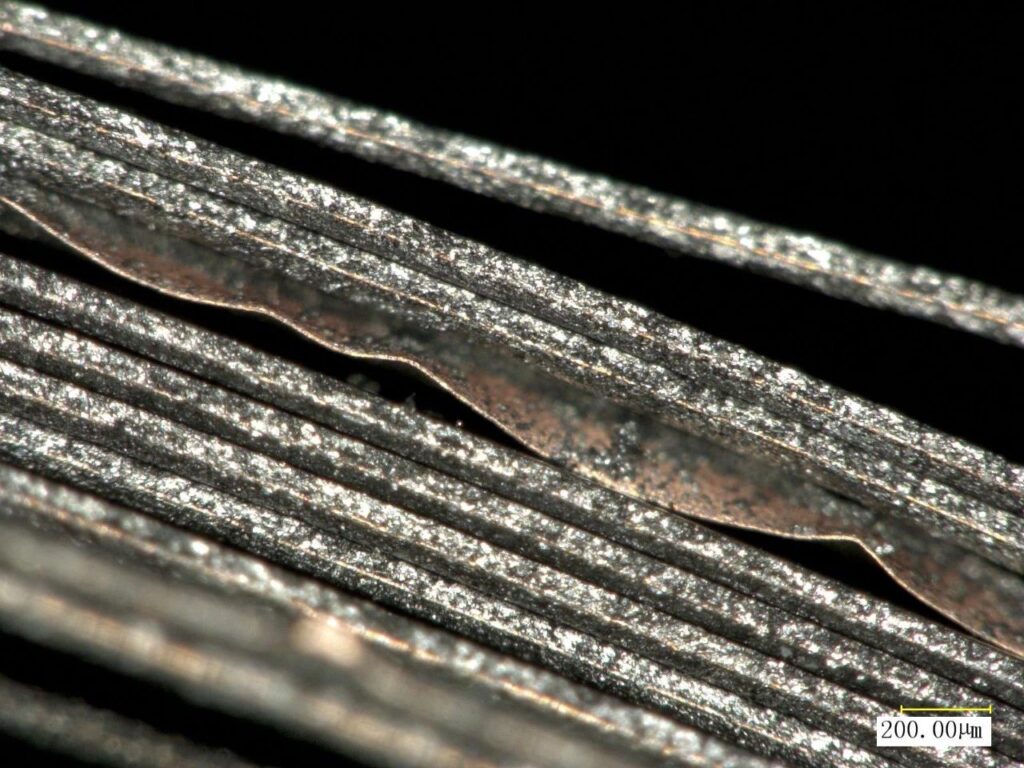
When the negative electrode disc is slit, wavy edges are formed and the cutting coating is peeled off due to the inappropriate amount of overlap and pressure of the cutter.