Lithium battery manufacturing 30 process decryption: from the coating accuracy to the activation of the formation of process control points
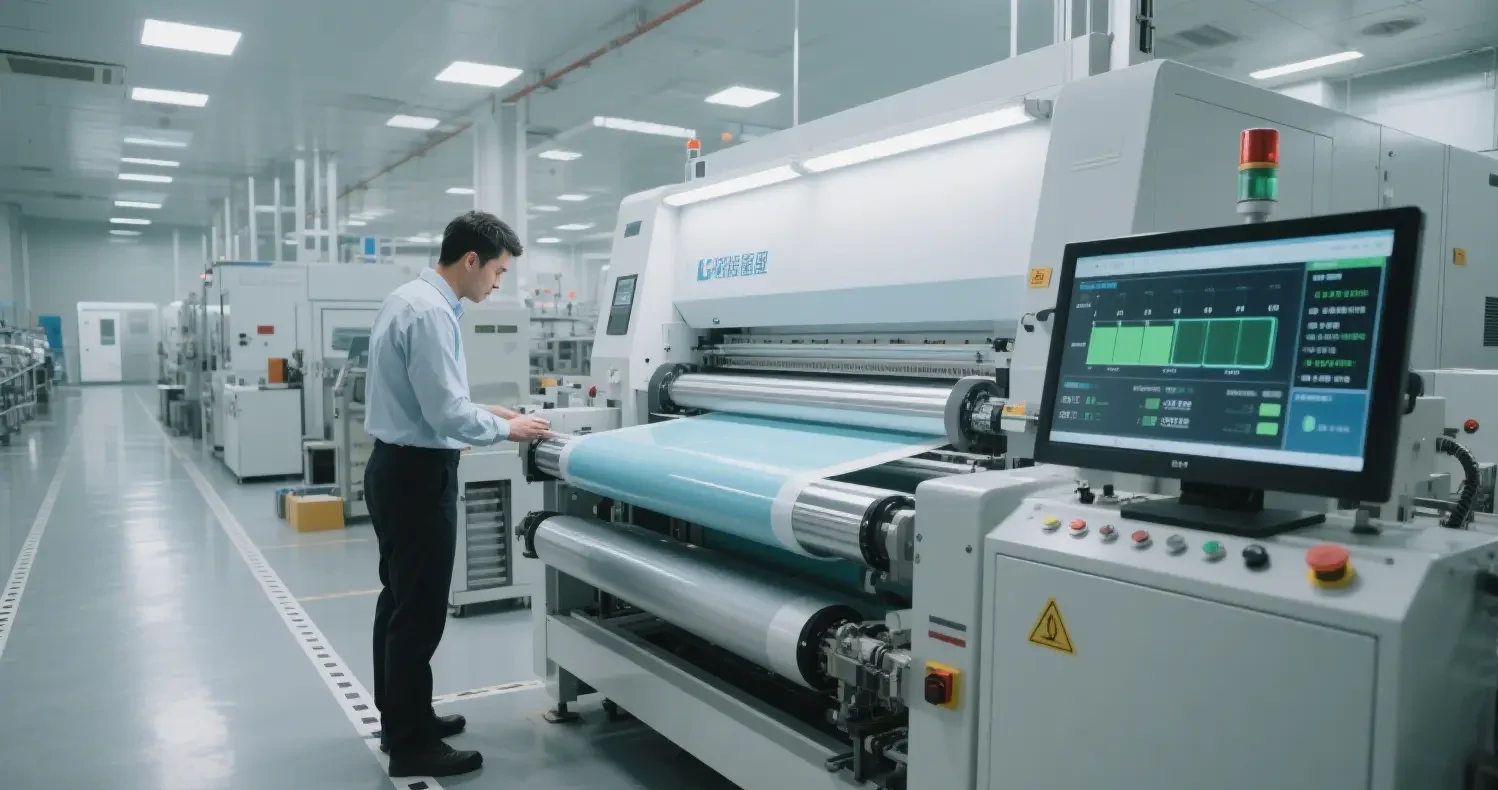
🔥 Front-end pole piece fabrication: the battleground for 75% of defect sources
✅ Golden parameter matrix for slurry preparation
Material system | Viscosity range | solid | Particle Size Requirements | degree of vacuum |
---|---|---|---|---|
NCM Positive | 3500±500mPa·s | 78±2% | D50≤8μm | ≤-0.085MPa |
Graphite Anode | 2500±300mPa·s | 52±1% | D50≤20μm | ≤-0.09MPa |
Fatal Trap: Anode slurry temperature >30℃ will lead to PVDF molecular chain breakage, bonding force decreased by 40%.
⚙️ Battery coating process life and death line
Speed and precision game:
High-speed coating (45m/min) need to match the double-sided simultaneous thickness measurement system (accuracy ± 0.5μm)
Transfer roller speed ratio 1.15-1.25, gap thinning 20-30μm anti-tail dragging
Drying zone control:
Positive: 105℃(Zone1)→115℃(Zone2)→95℃(Zone3) Moisture≤1500ppm
Negative: 90℃(Zone1)→100℃(Zone2)→85℃(Zone3) Moisture≤2500ppm
NDT Battery Case: Moisture exceeds 300ppm → Black spot rate soared 8 times after 200 cycles4
🛡️ roll pressing/slitting explosion-proof program
Hot pressing process: positive compaction density 3.4-3.8g/cm³ (cold pressing rebound rate ↑300%)
Slitting burr control: Y-direction burr ≤ 1/2 diaphragm thickness (measured >12μm direct scrap)
Recommended equipment: Pilot Intelligent G16 Slitter (burr control ±3μm)
⚙️ Middle core synthesis: 0.01mm alignment error = thermal runaway
⚡ Winding vs. stacking ultimate showdown
parameters | Winding process (cylindrical/square) | Laminating process (soft cover) |
---|---|---|
efficiency | 12PPM (BYD Blade Battery) | 0.5s/piece (Honeycomb Energy Flying Stack 2.0) |
Alignment accuracy | ±0.3mm | ±0.15mm |
Tension control | 0.08-0.15MPa | 0.05-0.1MPa |
Lesson learned: negative electrode coating less than 0.5mm → charging lithium precipitation → needle puncture through the diaphragm
🧪 The devil’s details of the injection process
Electrolyte infiltration equation:
Liquid injection volume (ml) = core pore volume × 1.15 + diaphragm absorption
Moisture stranding program:
Glove box dew point ≤ -45°C (GREE G-HBOX Pro measured value)
Helium leakage detection rate ≤ 2 × 10-⁷ Pa-m³/s (Precision Measurement Electronics HEL-800)
NDT Warning: Moisture >50ppm will trigger CMC dissociation → graphite layer stripping black slag

🔋 Back-end formation testing: SEI films make the difference between life and death
⚡ Chemistry Process Core Code
SEI Membrane Growth Control:
Optimal Current: 0.02C
Temperature Window: 45±1°C
Voltage Slope: dV/dt ≤ 5mV/min
Fatal Error: >0.05C current causes SEI membrane to cleave → 38% capacity degradation over 500 cycles
📊 Intelligent Strategies for Compartmentalization and Sorting
Filtering dimensions | threshold | Exclusion criteria | Equipment program |
---|---|---|---|
pressure drop | ΔV>10mV/24h | Microshort circuit risk | High temperature aging room + AI monitoring |
internal resistance | Deviation from the mean >5% | thermal runaway hazard | HIOKI 3560 Tester |
capacity | <95% of nominal value | Breach of batch consistency | Ranch Electronic Separation Cabinet |
BYD data: Battery packs with >3% difference in internal resistance → 60% shorter cycle life
🔋 Back-end formation testing: SEI films make the difference between life and death
⚡ Chemistry Process Core Code
SEI Membrane Growth Control:
Optimal Current: 0.02C
Temperature Window: 45±1°C
Voltage Slope: dV/dt ≤ 5mV/min
Fatal Error: >0.05C current causes SEI membrane to cleave → 38% capacity degradation over 500 cycles