Practical methods and points to note for improving the mixing uniformity of lithium-ion battery pastes
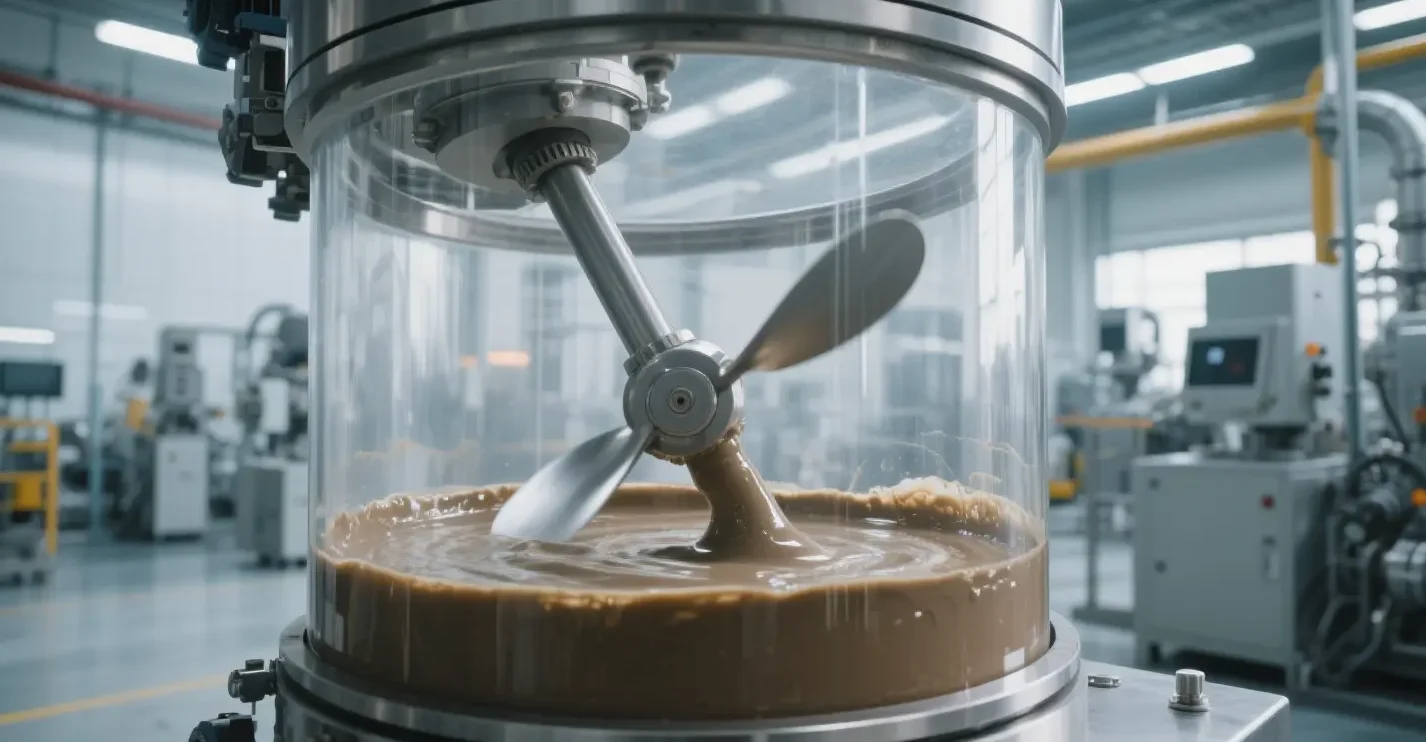
Abstract:This paper introduces in detail the effective methods to improve the mixing uniformity of lithium-ion battery slurry, covering planetary stirring, vacuum stirring, multi-stage stirring, high-speed dispersion, constant temperature stirring and optimization of stirring parameters. At the same time, it analyzes the key matters that need to be paid attention to in the actual application, which provides practical reference for battery buyers and manufacturers to optimize the process and improve the performance of the battery.
I. Why is the homogeneity of slurry mixing critical?
The performance of lithium-ion batteries, such as capacity, cycle life and safety, depends largely on the mixing quality of the battery slurry. Mixing link is not good, the active substance, conductive agent and binder dispersion is not uniform, will directly lead to high internal resistance of the battery, fast capacity degradation, and even localized overheating and other problems. For enterprises purchasing batteries, choose to master the uniform mixing technology suppliers, can reduce the product failure rate from the source.
II. Six methods to enhance the uniformity of lithium-ion battery slurry mixing
(i) Planetary stirring method: a powerful tool to deal with high-viscosity slurry
Working principle: the stirring paddle does rotation and spinning movement at the same time, like the planets rotating around the sun, covering every place in the slurry container in an all-round way. Core Advantage: Highly efficient in handling high viscosity slurry, avoiding sedimentation and stratification, especially suitable for mixing of anode slurry (e.g. NCM, LFP system). Operation key: Adjust the rotational speed and autorotation speed according to the viscosity of the slurry, generally the rotational speed is 50-200rpm, the autorotation speed is 500-1500rpm, and the mixing time is controlled at 30-60 minutes.
(ii) Vacuum stirring method: reduce air bubbles and improve battery consistency
Working principle: stirring in a vacuum environment reduces the air content in the slurry and makes the combination between particles tighter. Core Advantage: Reduce the risk of micro-short-circuit caused by air bubbles inside the battery, and improve the cycle performance and batch consistency of the battery. Operation key: control the vacuum degree between – 0.06 and – 0.09MPa, synchronize the vacuum time with mixing to avoid introducing air by breaking the vacuum in the middle.
(iii) Multi-stage mixing method: gradual and uniform dispersion
Working principle: adjust the mixing intensity and time in stages, from pre-mixing at low speed to dispersing at high speed, and gradually improve the uniformity. Core Advantage: Reduce the risk of one-time mixing failure, especially suitable for complex composite pastes with complex composition (such as the system of adding multiple conductive agents).
Operation key:
The first stage (pre-mixing) mixes with low speed (300-500rpm) for 10-15 minutes;
The second stage (dispersing) increases the speed to 800-1500rpm for 20-30 minutes;
The third stage (homogenizing) mixes with medium speed (500-800rpm) for 10-20 minutes.
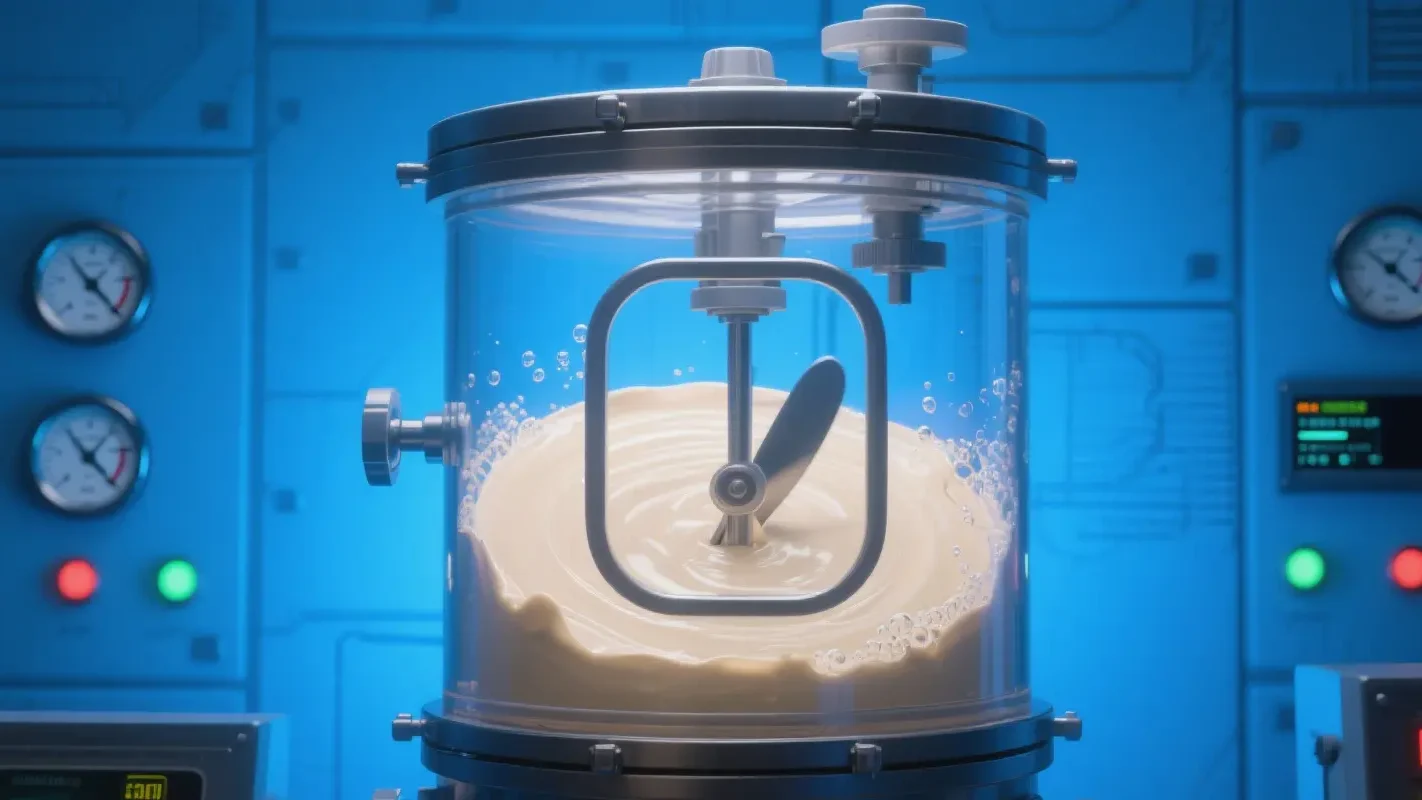
(iv) High-speed dispersion method: quickly break the particle agglomeration
Working principle: Strong shear force is generated by the high-speed rotating dispersing disk to break the agglomerates of active substances or conductive agents. Core advantage: high dispersion efficiency, can quickly deal with easy to agglomerate nanomaterials (such as carbon nanotubes, graphene). Operation key: the rotational speed is controlled at 2000-3000rpm, and the time should not be too long (5-15 minutes) to prevent the particles from being over-crushed and affecting the performance.
(v) Constant Temperature Stirring Method: Key to Stabilize Slurry
Working Principle: Stirring at a constant temperature to avoid changes in slurry viscosity caused by temperature fluctuations. Core Advantage: Keep the viscosity of the slurry stable to ensure the thickness uniformity of the subsequent coating process. Operation key: control the temperature according to the type of slurry (usually 25-35℃ for positive electrode slurry, 20-30℃ for negative electrode slurry), use water bath or oil bath heating to ensure uniform temperature distribution.
(vi) Optimize stirring parameters: details determine success or failure.
Stirring speed: 500-1000rpm for low-viscosity slurry (e.g. anode graphite slurry), 1000-2000rpm for high-viscosity slurry, too high will lead to slurry splashing and overheating. Stirring Temperature: Determine the optimal range through experimentation, for example, slurries with PVDF binder, too high a temperature will lead to binder decomposition. Vacuum level: adjusted according to the boiling point of solvents, solvents with low boiling point (e.g. NMP) need to control the vacuum level to avoid excessive volatilization affecting the solid content of the paste.
III. The actual operation of the 7 points of attention
(a) Select the method according to the material characteristics
Lightweight, easy to float conductive agent (such as carbon black), it is recommended to use high-speed dispersion method to break up, and then mixed with planetary stirring. high density active substances (such as some NCM materials), need to extend the mixing time or with tilting mixing paddle to prevent precipitation.
(ii) Equipment selection should match the production needs
Small batch trial production: choose laboratory-grade vacuum planetary mixer (5-50L). Large-scale production: prioritize continuous multi-stage mixing equipment, with online viscosity monitoring system. Regular inspection: wear and tear of mixing paddles will affect the uniformity, it is recommended to calibrate the paddle gap every 3 months.
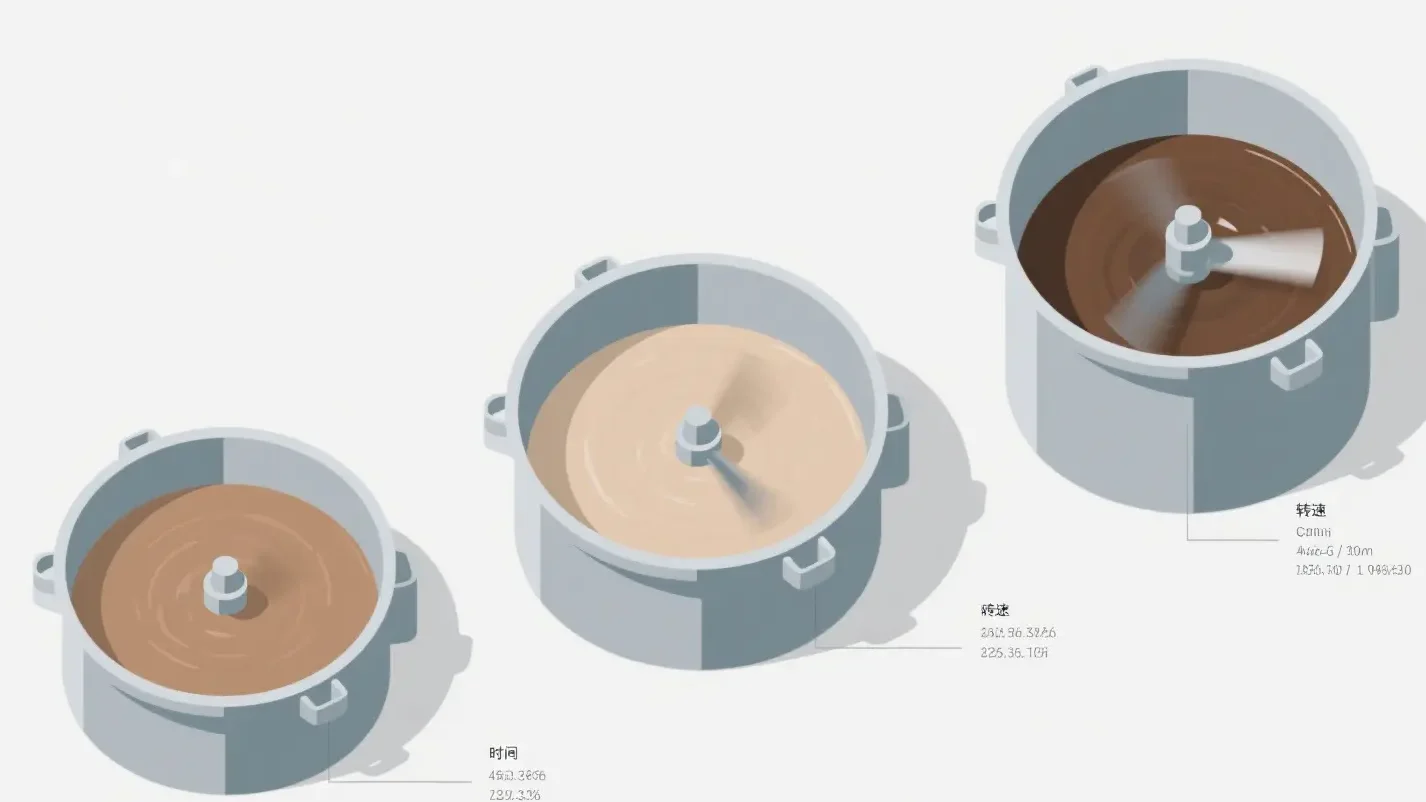
(iii) The order of mixing should not be messed up.
Correct order of adding materials: solvent → binder → conductive agent → active substance. For example, for anode slurry, first add deionized water, dissolve CMC, then add SBR, then add carbon black, and finally add graphite, and stir for 10-15 minutes between each step.
(iv) Verify the mixing effect with data
The slurry after mixing should be tested:
Particle size distribution (D50 fluctuation should be less than 5%)
Viscosity (deviation of the same batch should be controlled within ±10%)
Solid content (the error should not be more than 0.5%)
(v) Control the mixing environment
Humidity: water-based slurry (such as negative electrode) should be controlled at 30-50% RH to prevent moisture absorption. Cleanliness: the mixing workshop should reach 100,000 cleanliness to avoid dust pollution.
(vi) Operators need to be trained at
focusing on training: equipment parameter setting, handling of abnormal situations (such as how to protect the slurry in case of a sudden power outage), and cleaning specifications (to avoid cross-pollution of different slurries).
(vii) Continuous optimization of mixing process
There may be differences in different batches of raw materials, and the parameters need to be adjusted regularly through small tests. For example, the optimal mixing time should be re-tested after changing the supplier of active substances.
Fourth, summarize
For battery buyers, understanding lithium-ion battery slurry mixing technology can more accurately assess the supplier’s production strength. Homogeneous slurry is the foundation of high-performance batteries. Choosing the right mixing method, controlling the key parameters, and paying attention to the material characteristics and operational details can stably improve the quality of batteries. With the development of technology, intelligent mixing equipment (such as AI adaptive parameter adjustment system) will further improve the mixing efficiency and consistency, which is also an important trend in future battery production.